New Switches & Crossings Lubrication Solution at London Waterloo Delivers Major Cost Economies for Network Rail
- Nov 27, 2023
- Rail
A requirement to reduce track maintenance at London Waterloo station has resulted in the innovative re-engineering of a friction management dispenser by L.B. Foster Friction Management - part of global infrastructure solutions provider L.B. Foster Company - that is now delivering major cost economies for Network Rail.
London Waterloo is Britain’s largest and busiest station, with over 41 million passenger entries/exits in 2021/22. Switches and crossings (S&C) on the entry/exit to the station’s 19 passenger platforms experience very high levels of traffic. This has resulted in high rates of Rolling Contact Fatigue and 053 maintenance inspection defects, causing a correspondingly high turnover of S&C units, as well as increased maintenance and unit replacement cost for Network Rail.
Jonathan Paragreen is General Manager at L.B. Foster Friction Management. He explains: “The switch and crossing defects are primarily caused by track curvature on the entry/exit to the platforms, which increases the lateral forces suffered on the rail. We were approached by Network Rail to review the situation and to identify a more efficient and cost-effective lubrication solution.
“Our ultimate goal was to reduce the requirement for maintenance teams to work trackside, whilst extending the life of the switches and crossings. The resultant collaboration has seen exceptional results, both in terms of cost savings and enhanced operative safety through reduced time trackside.”
Historically, Network Rail had introduced a maintenance heavy lubrication regime to combat the large number of S&C defects at London Waterloo. A number of automatic lubrication systems were installed on the S&C at the station; these twisted on and dispensed grease at a set interval (powered by a battery pack) and typically last a maximum of 28 days. This makes them both labour intensive and costly, as a system is required on both the left and right rail respectively, whereas a typical mechanical or electric lubricator can supply both rails through a piped/blade system.
It is easy to see the cost savings over time and also the Maintenance Standard Task reduction in the trial area alone.
Neil Cassidy, Project Manager at Network Rail
Since the automatic lubrication systems were installed there had been a large reduction in S&C defects. An examination of both P8 failures and 053 defects showed the effectiveness of the lubrication. The benefits of the lubricant were cited as one of the contributing factors in the reduction of defects, along with a proactive S&C grinding programme to increase the lifespan of the S&C units.
In early 2022 Network Rail received a request from the Track Authority (TA) to look at ways of reducing Maintenance Standard Tasks (MSTs). The automatic lubrication systems at London Waterloo formed a large part of the Lubricators’ work bank. The TA request provided a natural starting point from which to look at potential time and attributed cost savings, as the automatic lubrication systems were the most onerous asset to maintain.
Network Rail contacted L.B. Foster concerning how to reduce the maintenance cycle. L.B Foster’s team proposed an innovative new design of hydraulic lubricator with a vertical lubricant reservoir that could be installed trackside, even in restricted spaces such as those experienced at London Waterloo.
L.B. Foster reimagined its existing PW Series hydraulic lubricator for use at London Waterloo. The PW offers a number of specific advantages over mechanical lubricators, providing an economic and effective method for distributing grease to the rail. The PW is available in 12.5kg and 37.5kg chamber capacities.
The trial 12.5kg PW unit was partially buried trackside, allowing trains to pass unhindered. As the train wheels pass over the system’s plunger it is depressed and activates a pump, which pushes grease to the applicator bars on the rail. The grease is picked up by the train wheels and is applied over a pre-agreed distance on the rail.
A set of points was selected (1564B) for the six month trial, with a hoped-for lubricant pickup to cover platforms 1,2,3 and 4 and the associated automatic lubrication systems on S&Cs 1564B and 1506 (see station diagram). The result was that both automatic lubrication systems were removed from 1564B, with good grease line noted. The automatic lubrication system was also removed from 1506. Network Rail is subsequently looking to install a further L.B. Foster PW unit on 1564A pts to trial removing more automatic lubrication systems in the Waterloo area.
Network Rail identified a projected cost saving of £18,546.48 over five years where a single 12.5kg capacity PW was installed on two sets of switches and crossings, versus a comparable install of three automatic lubrication systems.
For more information on L.B. Foster’s full range of friction management solutions visit Trackside Gauge Face Lubrication or download the Case Study for Waterloo station’s lubrication upgrade below.
Case Study
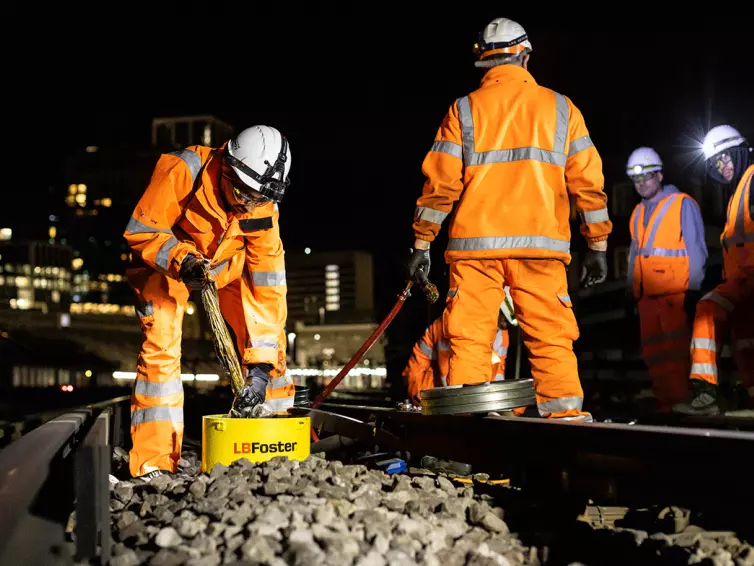